Why The Energy Production Industry Needs a Continuous Emissions Monitoring Solution
Ready to build your IoT product?
Create your Particle account and get access to:
- Discounted IoT devices
- Device management console
- Developer guides and resources
Political and voluntary initiatives regarding the mitigation of methane emissions have come squarely into focus since the 2021 United Nations Climate Change Conference held in Glasgow.
For sectors that produce methane as a byproduct of their processes (especially oil and gas production), this signals a major change in how methane and other greenhouse gas emissions must be detected, mitigated, and prevented—yet the industry is still searching for the best way to comply.
Because most methane-monitoring systems rely on imprecise measurements or intermittent testing, continuous emissions monitoring facilitated by Internet of Things sensors across entire capital deployments will be no less than vital for staying ahead of the ever-tightening regulatory environment.
In this article, we’ll discuss:
- Why methane emissions monitoring has taken on a renewed importance following the COP26 conference
- Why periodic emissions measurements fail to accurately detect excess emissions
- Why and how IoT will bring emissions monitoring into a more transparent and reliable future
Article Summary
Methane emissions monitoring and mitigation are a key concern for oil and gas companies as regulatory pressure increases around the world. Between the pledges made at COP26 and voluntary emissions reporting standards like the Oil and Gas Methane Partnership Framework, energy producing companies will need to shore up their emissions monitoring, measuring, and mitigation capabilities across their deployments.
Many existing emissions monitoring technologies will be insufficient to meet the methane reduction goals laid out by regulators. They are either too intermittent to provide realistic emissions measurements, or are too expensive to deploy across an entire capital stack, resulting in missing data.
IoT can facilitate continuous emissions monitoring because its relatively inexpensive to deploy across geographically dispersed areas and diverse equipment types.
IoT solutions can offer global connectivity to manage remote assets, connect disparate equipment types and compile different types of data, push over-the-air updates to improve device performance, and remotely control assets down to the component level in case immediate shutdown is required.
Methane Emissions Monitoring Comes Into Focus With COP26 and Voluntary Initiatives
The 2021 United Nations Climate Change Conference, recent government mandates, and voluntary initiatives implemented within the oil and gas industry over the last decade have all made it apparent that methane emissions are in the crosshairs of both private and public-sector organizations as a key target for monitoring and reduction.
Where past emissions reduction efforts focused mostly on carbon dioxide, newer projects are highlighting methane and other greenhouse gases. Of note, current rules for methane emissions in the U.S. only apply to sources built or modified after 2015, leaving more than 90% of the nation’s sources unregulated.
One of the major outcomes of COP26 was that the U.S. and more than 90 other countries signed a pledge to reduce methane emissions to 30% below 2020 levels by 2030.
As a result, the U.S. Environmental Protection Agency intends to limit the methane coming from roughly 1 million existing oil and gas rigs across the country. The Biden administration estimated that this new ruling will cover around 75% of all methane emissions.
Although these agreements signaled a major step forward in improving emissions monitoring and reduction around the world, it is important to remember that they originated against a backdrop of multiple voluntary methane reduction initiatives spearheaded by oil and gas companies. In fact, a recent report from Highwood Emissions Management detailed more than 20 voluntary industry-specific initiatives to take steps toward targeting, achieving, and showing results for emissions reduction.
One of those initiatives is the Oil and Gas Methane Partnership 2.0 Framework. Originally launched in 2014, the OGMP was a major voluntary initiative that gave companies a credible method of reporting and addressing methane emissions. The framework was updated in 2020 to improve reporting standards and share best practices developed since its inception.
Looking at the big picture, it’s apparent that the way oil, gas, and large industrial companies are monitoring and reporting emissions must improve the overall data quality in their reports.
The Environmental Defense Fund has found that oil fields in the U.S. are leaking 60% more methane than the Environmental Protection Agency had estimated. Reduction efforts must start with more accurate monitoring of greenhouse gas emissions, and only then can there be actionable methods of mitigation.
Learn what four IoT and emissions monitoring experts here at Particle had to say about the impact of COP26 on emissions monitoring.
Why Existing Emissions Monitoring Technologies Fail to Control Emissions
In a 2015 technical support document examining some of the most common methods of detecting and measuring methane emissions, the EPA noted that while each method could be effective, most had flaws that made accurate emissions detection difficult.
Traditional leak detection methods such as toxic vapor analyzers or organic vapor analyzers work well for small facilities but are expensive and cumbersome to install in large facilities or over geographically dispersed locations.
Since hydrocarbons in greenhouse gas emissions absorb infrared light, another monitoring method makes use of infrared remote equipment leak detectors, of which there are two types:
- Passive instruments that scan an area to produce images of equipment leaks from a source
- Active instruments that point or aim an infrared beam toward a potential source to indicate equipment leaks
Although these infrared “cameras” can reliably detect leaks and survey an entire facility relatively easily, they are capital-intensive and cost-prohibitive if deployed over multiple locations.
Infrared laser systems can reliably pinpoint leaks and are more cost-effective than infrared cameras. However, because the laser has to be pointed at each individual part of a machine, screening equipment for leaks using this approach takes more time. Additionally, if multiple leaks are present, the system will be unable to accurately detect the source.
While forms of aerial surveillance such as drones, planes, and satellites can be useful for capturing the global magnitude of methane emissions from large point sources, they rely on a snapshot approach that compromises data accuracy.
Why Traditional Emissions Monitoring Techniques Have Drawn Criticism
By 2021, the EPA and its overseas equivalents were ready to add the weight of regulation to what was previously a mostly voluntary effort to reduce methane and other greenhouse gases. In the U.S., this move was largely prompted by claims that the EPA was vastly underestimating emissions levels from the oil and gas industry.
As detailed in a report from E&E News, the EPA currently calculates methane emissions by multiplying the number of potentially leaky components—like valves and thief hatches on well heads and storage tanks—by an estimate of the average emission rate for each part.
According to critics, this sort of “bottom-up” approach underestimates emissions because it only considers a small sample size of wells and facilities, whereas a “top-down” approach using satellites or aircraft to take measurements of methane emissions around a site would be more effective. In some cases, the latter method finds up to twice the amount of methane and other greenhouse gas emissions.
Moreover, critics of the EPA’s current methodology have pointed to outdated equipment and methods that they believe are compounding data accuracy issues. Specifically, the approach used by the agency to make estimates is based on industry self-reporting and a single study that’s decades out of date, and the types of machinery used in oil and gas production have changed significantly due to the natural gas, shale, and fracking boom.
Improving emissions data quality and detection has to start at the edge—namely, the equipment in the field—and work its way back through an integrated IoT ecosystem that provides reliable connectivity to the cloud. Using this setup, analysts and technicians can leverage data to make faster and more accurate decisions.
Continuous Monitoring, Remote Control, and Preventative Maintenance: Why Emissions Monitoring Needs IoT
Oil and gas companies that want to stay ahead of the regulatory curve, avoid fines and lawsuits, and get certified in OPMG and other third-party standards are realizing that they can’t rely on outdated and inaccurate methods of emissions monitoring—but they may not realize that more recent advances in methane leak detection via aircraft and other modern approaches still have deficiencies, such as:
- “Flyover” methods of methane detection are still intermittent, meaning they don’t give oil and gas producers or facility managers a way to track emissions in real time. As a result, leaks can subsist and even worsen between flyovers, going undetected until the next time someone takes an emissions snapshot.
- Many traditional methods of measuring methane emissions can’t distinguish between fugitive and vented emissions. They’re unable to reliably tell you if there’s a leak or if there’s just a concentration of normally vented emissions.
- If you need to deploy monitoring over wide geographic areas or large facilities, traditional emissions monitoring systems are generally cost-prohibitive.
- Detection and mitigation are still two different processes. If you detect a leak, a repair crew has to physically travel to the site to perform an assessment, shut down the equipment, and fix the problem, which can be particularly costly and time-consuming when the equipment is in a remote location.
- As different components, subassemblies, and assets are brought into the capital mix of oil and gas production, accurately monitoring their performance and condition requires built-in sensors that can track and aggregate different types of data to provide an all-encompassing view of your assets at the individual machine, site, and company level.
Continuous emissions monitoring solutions based on IoT technology can provide real-time insight into not only greenhouse gas emissions but also equipment performance and condition. For oil and gas companies as well as their solutions providers, these solutions offer a way to not only monitor equipment for rogue emissions but actually gain command over assets. Per the International Energy Agency, oil and gas companies can achieve a 75% reduction in their methane emissions when they use the right set of technologies.
One leading solutions provider in this space is Qube, which partnered with Particle to build the world’s first continuous monitoring technology for regulatory use. In a recent webinar, Qube COO Eric Wen and Particle Enterprise Account Executive Cyril Bernard made the case for IoT as a means of making truly continuous emissions monitoring a reality.
Prevent Leaks and Reduce Emissions
On-Demand Webinar
Join Particle Enterprise Account Executive Cyril Bernard and Qube COO Eric Wen to learn how IoT-connected emission monitoring systems make it possible to adhere to compliance standards and develop innovative solutions to help battle fugitive emissions and improve safety and environmental outcomes for operators.
- Learn how IoT improves capacity for the broader energy industry to protect the environment
- Understand the latest technologies to help meet your emission standards
- See how emission monitoring solutions reduce and repair leaks
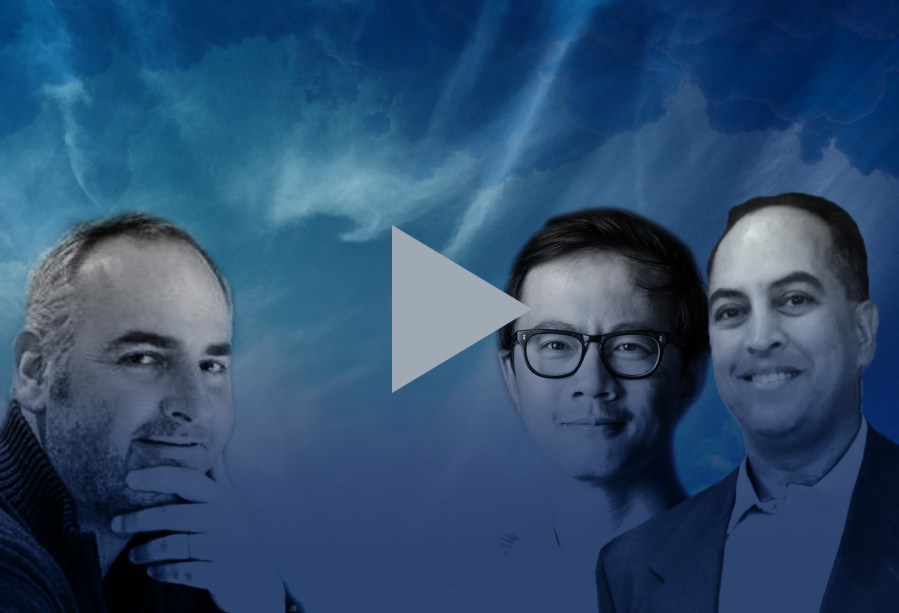
What makes IoT such an effective solution for the problem of emissions monitoring? Let's take a look at what Eric and Cyril had to say.
Gain More Control Over Assets
Although being able to detect methane and other greenhouse gas leaks is important, mitigation is the essential next step to truly reducing rogue emissions.
“The other kind of capability that's pretty important about IoT is you can actually monitor the equipment itself. So in addition to detecting leaks and detecting gases, you can actually look at the device activity across pumps, gauges, hydraulic systems, etc., and these can all be monitored using different types of sensors,” Cyril explained.
Continuously monitoring equipment down to the component and subassembly levels across a geographically dispersed deployment and a diverse array of assets is already a major step toward meeting industry standards like OPMG or government regulations derived from COP26 commitments—but according to Cyril, the critical point is being able to remotely control your assets.
“Say you have an emergency or problem and there’s a leak in one of your machines; you can actually turn machines on and off with IoT,” Cyril pointed out. “The connection between the physical and the cloud allows you to shut down malfunctioning equipment and stop leaks until you can send a repair crew to mitigate the bad situation.”
Track a Variety of Assets and Devices
With new assets being added to oil and gas companies' capital stacks, many energy producers are trying to manage a mix of legacy and modern assets.
As different types of equipment enter the mix, the number of different components, parts, and subassemblies that must be monitored and maintained grows continuously—and while modern assets may have built-in machine-to-machine communication capabilities, the real value comes from being able to extract and use asset data to drive condition monitoring and preventative maintenance.
With IoT, it becomes possible to attach sensors and actuators to nearly any component or machine for data collection. The data amassed from these hundreds or even thousands of different sensors can be sent to the cloud via cellular or Wi-Fi connectivity, then made available for human users to make better decisions about their equipment.
Because IoT-enabled devices all connect via an IoT gateway, removing the barriers created by machine-specific languages gives companies deeper insight into their capital mix.
Realize Global Connectivity
One of the major challenges associated with emissions monitoring is deploying and regularly updating the monitoring equipment itself. For many oil and gas companies, assets such as oil rigs out on the ocean and pipelines far from civilization are often difficult and costly to reach.
That means the decision between cellular vs. WiFi is critical for emissions monitoring. Both connectivity options have a part to play, and in some cases, using both makes sense.
IoT makes it possible to connect those assets with sensors and other edge devices, then upgrade them remotely through a cloud interface. This is where having a reliable connection to global cellular networks becomes a critical part of an enterprise IoT solution.
For example, Particle’s EtherSIM and EtherLink solutions provide reliable, “just works” connectivity to cloud solutions via cellular networks. In particular, EtherLink ensures that your assets maintain a high level of connectivity thanks to:
-
Intelligent delivery that allows you to send data with delivery confirmation and automatic retries using one line of code.
-
Real-time control through which you can establish and maintain real-time, encrypted tunnels for low-latency messaging.
-
Self-healing to automatically recover a lost cloud connection.
-
Built-in connectivity health-logging that facilitates automatic Device Vitals logging, reporting, and storage via the cloud.
No matter how remote your asset location, leak detection and mitigation start with a reliable connection among sensors, cloud, and people.
Push Over-the-Air Updates for Improved Remote Monitoring
Being able to push needed firmware updates to sensors that upgrade functionality or fix bugs helps ensure that your emissions monitoring capabilities are always at their full strength.
Because assets and their attached sensors are geographically dispersed, the only efficient way to upgrade all of them at once is to use OTA updates. Simply put, implementing OTA firmware updates refers to the practice of remotely updating the code on an embedded device.
“Using OTA updates without having to physically go to devices is a game changer for us,” Eric said. “A lot of our deployments are in very remote locations that are difficult to access or drive to. Having that ability to have a tool that is not only scalable and low-cost but has these kinds of fleet-managed services has been really valuable for us.”
Successful OTA updates require complex coordination between IoT hardware, device firmware, network connectivity, and an IoT device cloud. If any one of these pillars is not working properly, your OTA updates will either fail or brick your devices—which is where an integrated IoT solution becomes incredibly valuable.
With Particle, you can tightly integrate the following core components of an IoT solution:
-
Hardware. All Particle dev kits and systems-on-a-module support OTA updates right out of the box. Device and cloud-side safeguards are combined to ensure devices only receive compatible firmware that can run on their unique hardware platforms.
-
Device OS. Device OS—our embedded operating system that runs on all Particle devices—is architected to reliably and resiliently accept firmware updates from the Device Cloud.
-
Connectivity. OTA updates work seamlessly across Particle's suite of connectivity offerings. Devices connecting over Wi-Fi and cellular can receive firmware updates using our OTA feature set.
-
Device Cloud. The Device Cloud tightly integrates with Device OS to safely and effectively deliver OTA updates while also providing a variety of flexible management tools to choose how OTA updates should be applied based on need.
Given the importance of continuous emissions monitoring, oil and gas producers can’t afford to lose access to their devices due to failed OTA updates, and Particle can help ensure that won't happen.
Learn how Particle optimizes data for each transaction via our cloud by adopting IoT protocols that minimize data usage.
IoT Is More Accessible Than Ever
As Eric and Cyril pointed out, IoT is now more broadly accessible for most organizations than ever before.
In the past, implementing IoT often meant building in-house edge, connectivity, and software components or buying a patchwork of point solutions and trying to integrate them. The resultant cost and complexity made IoT projects risky for even the most well-resourced organizations, and many companies failed to find business value.
With subscription-based IoT solutions like Particle, the hard parts—including OTA updates, global connectivity, and access to hardware in the face of supply shortages—are handled. This makes it easier than ever to facilitate an IoT deployment on time and within budget.
Thinking of Building an IoT Product In-House?
The build vs. buy decision shouldn't be made without a clear picture of the total cost of ownership for each option. Use this free calculator to run scenarios and see if it makes more sense to build or buy.
It's become abundantly clear over the last few years that emissions monitoring needs to evolve in three core ways:
- It needs to be more closely tied to emissions mitigation.
- It needs to be continuous, not periodic.
- It needs to be transparent, with standardized data that can be meaningfully analyzed and isn't based on outdated studies or self-reported estimates.
IoT is the vehicle that will bring these new realities to the world of emissions monitoring by unlocking tomorrow's emissions monitoring capabilities today.