The Top 5 Applications For Industrial IoT
Learn how IoT is transforming industrial operations by making remote asset monitoring, over-the-air updates, and inventory management easier than ever.
Ready to build your IoT product?
Create your Particle account and get access to:
- Discounted IoT devices
- Device management console
- Developer guides and resources
The industrial Internet of Things connects machinery and devices at smart factories and other industrial sites where keeping equipment operational is critical to productivity and safety.
Companies use IIoT technology to automate previously manual processes and manage their assets remotely, yielding new efficiencies and cost savings—and the sector is growing rapidly, expected to generate between $1.4 trillion and $3.3 trillion by 2030 (26% of the total IoT market value).
In this article, we’ll consider five top IIoT applications:
- Asset tracking: GPS-enabled devices can track assets on the move, from vehicles to individual crates and boxes.
- Preventative maintenance: Connected sensors help predict needed maintenance for industrial machinery and other assets.
- Inventory management: IIoT devices are bringing increased visibility to supply chains and inventory for companies in the industrial sector.
- Remote monitoring and control: IoT sensors can perform some elements of assembly line inspectors’ role by checking machinery for performance issues or defects and alerting managers when there’s a problem.
- Employee and environmental safety: Companies are using connected sensors to help monitor equipment usage, site logistics, and worker safety, making regulatory compliance a simpler task.
The Top 5 Applications and Use Cases of Industrial IoT
The vast majority of industrial organizations—92%, according to some sources—have already adopted IoT solutions to improve monitoring, maintenance, and remote operations. Let’s take a closer look at five of the top applications for IIoT technology.
Asset Tracking
Using GPS technology, sensors installed in vehicles and shipping crates allow organizations to track assets—whether they’re sitting on a job site or traveling across the country. While radio frequency identification tags provide a viable solution in some use cases, cellular IoT sensors differentiate themselves by sending constant updates that allow managers to continually view assets’ progress along their journey.
For example, GPS-enabled IoT devices can equip rental companies with remote, real-time visibility into asset location and condition in the field. Companies can use this data to improve logistics planning and bolster customer care by optimizing pickups and returns.
Another common application of asset tracking is in fleet management. While onboard GPS is nothing new in industrial settings, cellular IoT sensors can add layers of data beyond location information to help track compliance with safety requirements, monitor vehicle status, send maintenance alerts, optimize routes and fuel consumption, and more.
Preventative Maintenance
In the past, “preventative maintenance” referred to periodic in-person service of a piece of machinery, but the addition of cellular IoT opens up new possibilities. For instance, instead of initiating truck rolls with human mechanics for time-based service, managers whose companies deploy IoT sensors can keep track of machines remotely.
These sensors monitor essential performance metrics in real time and send out alerts when problems are detected, transforming preventative maintenance into an agile and responsive process.
The resulting reduction in service calls can improve operational efficiency, reduce operating costs, and save tremendous amounts of time, effort, and money, when it comes to monitoring remote assets—which is particularly important when you consider that the average company today has 31% of its assets in the field.
Inventory Management
Visibility is the single most valuable commodity in inventory management, as blind spots often result in untold inefficiencies and billions of dollars in fiscal losses. Fortunately, recent technological advancements have made it possible to increase visibility using a connected IIoT solution.
Today, a small, 4G-connected microcontroller can identify, locate, and monitor a moving asset in real time from virtually anywhere on earth, while more robust and affordable IoT platforms allow data to be easily received, organized, and analyzed via the cloud.
Moreover, automated alerts and event reporting allow companies to be agile and responsive in the face of supply chain and inventory disruptions. Thanks to the real-time insights provided by IoT sensors, organizations can keep needed consumables (e.g., fuels and lubricants) on hand to minimize downtime. The ability to track the condition of specific components empowers companies and their customers to order replacements ahead of time.
Learn more about how IIoT is revolutionizing supply chain management by downloading our free white paper.
Remote Monitoring and Control
Along with providing constant updates on the geolocation and mechanical status of industrial machinery, IIoT sensors offer the power to remotely change settings, activate equipment, or halt processes when the need arises. For example, if a water pump breaks and starts to leak, you can receive an alert and engage shutdown protocols right from your device, regardless of location.
This functionality is especially useful for assets located in hard-to-reach areas, as sending a technician to a distant location can be expensive and time-consuming—particularly when the only action needed is a simple settings tweak or standard reboot.
In manufacturing applications, remote monitoring connections are typically linked to programmable logic controllers. This gives managers remote access to reports and other logged data, along with the ability to send commands directly to machines or deliver instructions to a facility’s human operators.
Connectivity is key for remote machines and assets. Learn how IoT protocols play a role in transmitting useful data between the edge and your cloud.
Examples of Industrial IoT in Action
Service Thread
Service Thread—a leading American manufacturer of commercial thread and yarn— houses more than 3,000 spindles (operating positions) across 115,000 square feet of floor space and 24 different machine types at its factory in Laurinburg, North Carolina.
After embedding IoT microcontrollers into its spindle machines, Service Thread has seen significant improvements in machine operations and efficiency. In addition to providing continuous machine monitoring capabilities, these smart devices transmit timely alerts regarding problem components. The end result: long-term savings in operating and maintenance costs.
FieldIntell
FieldIntell is an end-to-end cloud platform for managing and optimizing logistics and highly distributed asset ecosystems in sectors with industrial assets located in remote areas, such as oil and gas, mining, and agriculture.
Companies within these sectors often need to send out employees to check, fix, and sometimes shut down equipment, which can be expensive and time-consuming. In response to these challenges, the FieldIntell IoT solution—built on Particle’s platform—makes it easy to connect to, collect, and control asset information anytime and from anywhere.
For example, one of FieldIntell’s mining customers requires its machines to run 24/7. With FieldIntell, the customer always knows not just these assets’ locations, but their current condition down to the component level.
Because the solution can integrate with the mining company’s enterprise resource planning system, work orders for maintenance are automatically generated when a component needs to be replaced.
Amper
Amper provides IoT-based solutions that grant shop floor visibility and allow managers to respond to issues in real time. Its sensors bypass the need for PLC integrations, attaching directly to a machine’s power supply and allowing immediate access to operational analytics.
Particle helps Amper deploy machine-monitoring solutions on factory floors for precision manufacturers, mostly geared toward preventative maintenance. With Amper’s solutions, manufacturers can capture machine utilization and uptime data, identify the root cause of downtime, gain visibility into operations, and automatically notify stakeholders when a machine goes down.
How FieldIntell is making industrial equipment monitoring simple
Case Study
FieldIntell was working to build IoT-enabled solutions to help companies in capital-intensive industries like oil & gas, mining, and agriculture monitor and control their remote assets in real-time.
Their original IoT hardware provider failed to innovate, leaving FieldIntell scrambling to find another solution.
Particle's certified hardware, flexible operating system, global connectivity and robust fleet management capabilities helped FieldIntell rebuild their products quickly and deliver a superior end user experience.
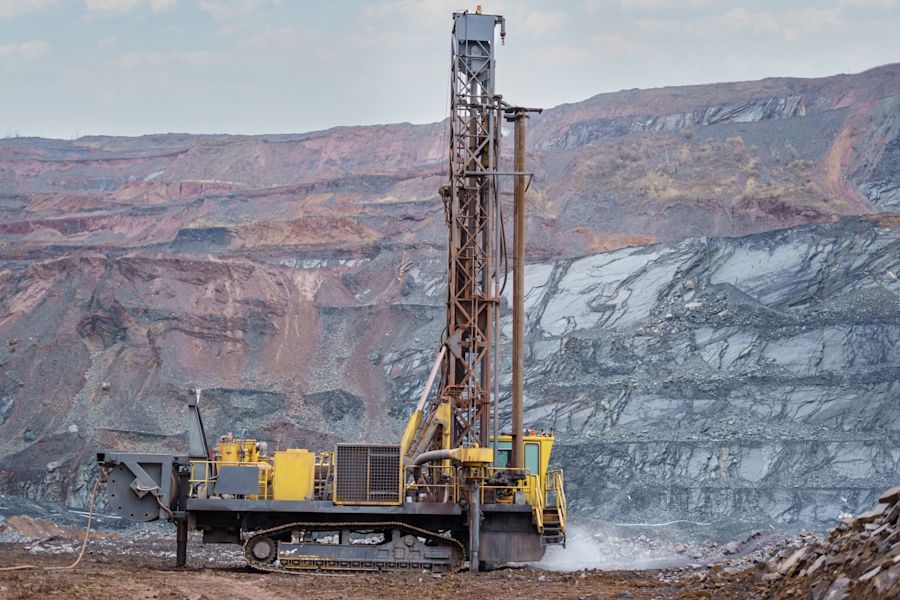
How IIoT Applications Impact Industrial Automation
IIoT applications are having a tremendous impact on furthering industrial automation (in other words, using computers to monitor and control machines and industrial processes rather than relying solely on humans). When industry leaders turn to IIoT solutions, they can:
Reduce the Impact of Labor Shortages
Labor shortages are common in the manufacturing industry. Using IIoT sensors can reduce the number of human personnel needed to check and service machines, particularly in remote locations. In addition, supply chain and warehouse automation can reduce the need for human oversight while increasing efficiency. In fact, the use of robotics and other automation has the potential to reduce manufacturing and labor costs by 25% to 30%, according to a recent report.
Automate Routine Tasks to Limit Human Contact
Since the COVID-19 pandemic began, limiting contact between employees has come to the forefront as an immediate priority and a serious safety concern. The pandemic accelerated the growth of IIoT across industries, with 77% of surveyed organizations now deploying at least one IoT project—and according to research, businesses that adopted IIoT automation were impacted less negatively by the pandemic than those that were more resistant to digital transformation.
Make Remote Equipment Upgrades With Over-the-Air Updates
When machines need firmware upgrades, remote monitoring and control systems provide a way to deliver these without needing to send a human to the site. Over-the-Air updates make it easier to respond rapidly to security vulnerabilities and secure your IoT devices.
You can also swiftly add new software features without the need for physical recalls or truck rolls to manually update devices. Particle’s platform is uniquely positioned to provide industry-leading OTA update services for embedded devices.
Contact us today to find out how Particle can help you get a headstart on developing industrial equipment monitoring solutions for your business.